The Expertise of a Plastic Mould Maker: Driving Innovation in Manufacturing
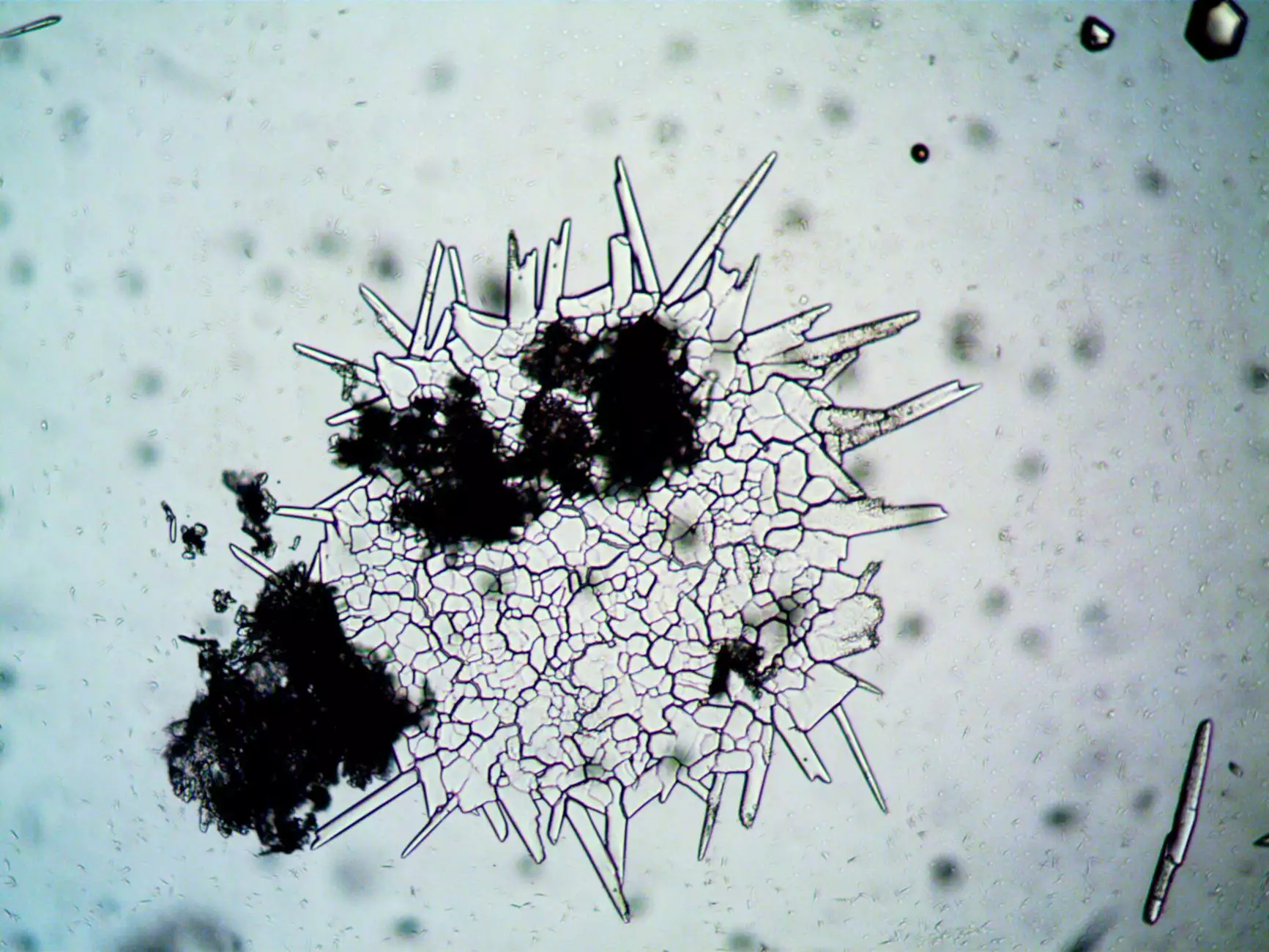
In today's fast-paced industrial landscape, businesses across various sectors are constantly seeking ways to enhance efficiency, reduce costs, and improve product quality. One of the pivotal elements in achieving these goals lies in the capability of a plastic mould maker. This article delves deep into the world of plastic mould making, exploring the multifaceted aspects of its significance, processes, and the benefits it brings to businesses.
Understanding the Role of a Plastic Mould Maker
A plastic mould maker is an expert who specializes in designing and manufacturing molds used for plastic injection. These molds are critical in the production of various consumer goods, automotive parts, and industrial components. The precise craftsmanship required in mold-making can significantly influence the overall quality of the final product.
The Importance of Plastic Injection Moulds
Plastic injection moulds are essential for a variety of reasons:
- Precision: High-quality moulds ensure that the produced parts are consistent and meet stringent specifications.
- Efficiency: Well-designed molds optimize the production process, reducing cycle times and waste.
- Cost-effectiveness: Investing in durable molds can lower long-term production costs by minimizing defects and rework.
- Flexibility: Mould makers can create customized solutions tailored to specific industry needs, supporting innovation.
The Process of Plastic Mould Making
The journey of creating a high-quality plastic mould involves several key steps, each requiring specialized knowledge and technical expertise.
1. Initial Concept and Design
The first phase in the process is the conceptualization of the mould. This includes:
- Client Consultation: Engaging with clients to understand their requirements and expectations.
- 3D Modelling: Using CAD software to create a digital representation of the mould design.
- Prototyping: Producing a prototype to test the design's feasibility and functionality.
2. Material Selection
Choosing the right materials for the mould is crucial. Factors to consider include:
- Durability: The selected material should withstand numerous injection cycles.
- Cost: Material costs must align with the budget while ensuring quality.
- Compatibility: The material should be suitable for the specific type of plastic being used.
3. Manufacturing the Mould
Once the design is finalized and materials are chosen, the actual manufacturing process begins. This includes:
- CNC Machining: Utilizing computer numerical control machines to achieve precise cuts and shapes.
- EDM (Electrical Discharge Machining): A technique used for intricate and detailed features.
- Assembly: Putting together the different components of the mould.
4. Testing and Quality Control
Before the mould goes into production, rigorous testing is conducted to ensure:
- Accuracy: Each component works as intended under production conditions.
- Durability: The mould can withstand the pressures and temperatures of the injection process.
The Benefits of Professional Plastic Mould Making
Companies like Hanking Mould, an esteemed plastic injection mould manufacturer, play a vital role in providing numerous benefits to businesses:
1. Enhanced Product Quality
By investing in advanced mould-making technology and expertise, plastic mould makers can produce high-quality products that adhere to industry standards. This distinction can significantly enhance a company's reputation and customer satisfaction.
2. Increased Production Efficiency
Professional mould manufacturers streamline the production process, reducing downtime and maximizing throughput. The precision of the moulds ensures minimal defects, which translates to lower costs and faster time-to-market.
3. Customization and Innovation
With the ability to create customized moulds tailored to specific needs, businesses can differentiate their products in the marketplace. This capability fosters innovation, allowing companies to introduce new and unique designs that meet evolving consumer demands.
Industry Applications of Plastic Moulds
The versatility of plastic moulds extends across various industries:
1. Automotive Industry
In the automotive sector, precision moulds are used to create components such as dashboard parts, panels, and reservoirs, ensuring they meet safety and functionality standards.
2. Consumer Electronics
Plastic moulds are pivotal in producing casings for smartphones, laptops, and other electronic devices. The high-demand nature of this sector requires moulds that can deliver consistent quality for mass production.
3. Medical Devices
The medical industry relies on moulds for various devices that require strict adherence to hygiene and safety regulations. Mould makers must keep up with the latest standards to ensure compliance.
4. Packaging
Packaging solutions, from containers to bottles, often use plastic moulds for efficiency and design flexibility. A skilled plastic mould maker can help businesses create innovative packaging that enhances product appeal.
The Future of Plastic Mould Making
The future of the plastic mould-making industry appears promising, with advancements and trends shaping its trajectory:
1. Sustainable Practices
As the world moves toward greater sustainability, the demand for eco-friendly moulding processes is on the rise. Sustainable materials and practices not only help in reducing environmental impact but also cater to a growing consumer preference for green products.
2. Automation and Technology Integration
Adopting automation in the mould-making process enhances precision and reduces production time. Technologies such as artificial intelligence (AI) and machine learning are becoming increasingly integrated, allowing for smarter production lines.
3. Innovations in Material Science
Developments in material science promise to create new opportunities. Innovative polymers that offer superior strength, flexibility, and resistance to wear will open new avenues for design and functionality.
Choosing the Right Plastic Mould Maker
When selecting a plastic mould maker, businesses should consider several factors to ensure they partner with the right industry leader:
- Experience: Look for mould makers with a proven track record in the industry.
- Capabilities: Ensure the manufacturer has the technical expertise and equipment to meet your specific needs.
- Quality Assurance: Check for certifications and quality control processes that guarantee the reliability of their products.
- Customer Support: Choose a company known for excellent customer service and support throughout the production process.
Conclusion
In conclusion, a professional plastic mould maker is an invaluable asset to businesses looking to excel in the competitive landscape of manufacturing. From automotive to consumer electronics, the significance of expertly designed moulds cannot be overstated. By prioritizing quality, innovation, and efficiency, companies like Hanking Mould exemplify the essential role that a mould maker plays in driving business success. As the industry continues to evolve, embracing new technologies and sustainable practices will undoubtedly set successful businesses apart from their competitors.
To explore more about high-quality plastic mould making and how it can benefit your business, visit hanking-mould.com.