Enhancing Your Business with Label Rollers: Unleashing the Power of Packaging
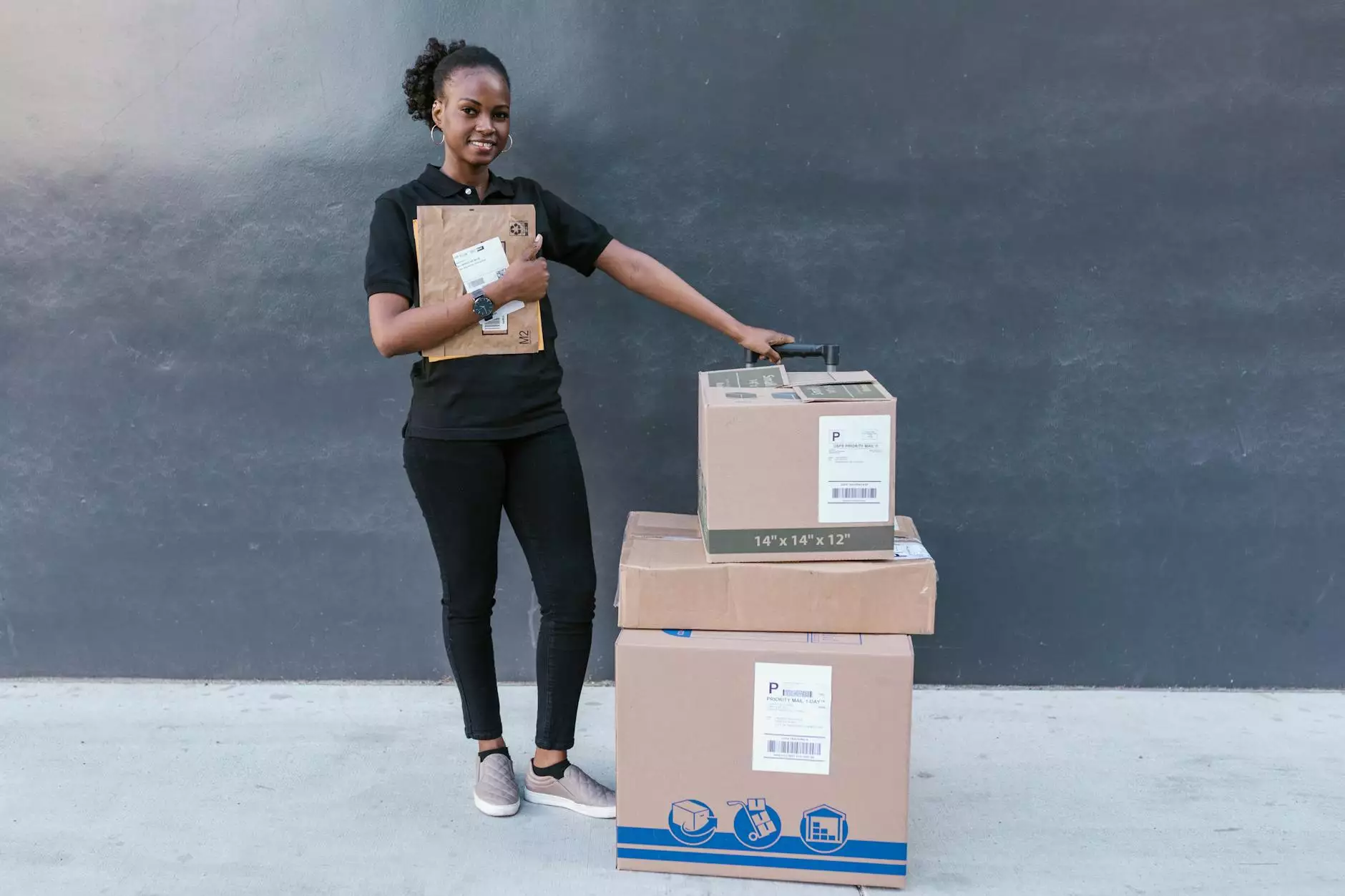
In today’s fast-paced business environment, efficiency and precision in packaging have become imperative for success. Among the vital tools in this domain are label rollers, which serve as a linchpin in the packaging process. These devices not only promote efficiency but also ensure that your products are presented in the best possible light. This article delves into the myriad benefits of label rollers, their various types, and how your business can leverage them effectively.
What Are Label Rollers?
Label rollers are specialized devices designed to streamline the application of labels on various products. They are particularly useful in industries that require a high volume of labeling, such as food and beverage, cosmetics, pharmaceuticals, and logistics. By enabling quick and precise label application, these tools improve productivity and reduce labor costs.
Benefits of Using Label Rollers
Utilizing label rollers brings several notable advantages to your packaging operations:
- Increased Efficiency: Manual labeling can be time-consuming and error-prone. Label rollers automate this process, allowing for faster production times.
- Consistency:Label rollers ensure that each label is applied uniformly, which is crucial for maintaining brand identity and aesthetics.
- Cost-Effective: By reducing labor input and minimizing errors, label rollers can significantly cut down operational costs.
- Versatility: These devices can work with a wide variety of label sizes and shapes, accommodating different products without the need for multiple machines.
- Enhanced Quality Control: Automated labeling minimizes the risk of mislabeling, ensuring that your products are always compliant with industry standards.
Types of Label Rollers
There’s a range of label rollers available, each designed for specific applications and industries. Here’s a closer look at some of the main types:
1. Manual Label Rollers
Manual label rollers are inexpensive and easy to use. Ideal for small operations or businesses that don’t require high-speed labeling, these tools allow operators to apply labels by hand, making them perfect for customized or small-batch production runs.
2. Semi-Automatic Label Rollers
Semi-automatic label rollers strike a balance between manual application and full automation. These machines often require the operator to load the labels but will automatically dispel and apply them, improving speed without requiring a significant investment.
3. Fully Automatic Label Rollers
For businesses looking for maximum efficiency, fully automatic label rollers are the ultimate solution. These sophisticated machines are designed to run continuously, requiring minimal human intervention. They are equipped with advanced features such as sensors to detect product positions and ensure perfect label placement.
4. Digital Label Rollers
Digital label rollers provide flexibility in label design and production, allowing for on-demand printing. This type is ideal for companies that frequently change labels or need to produce short runs with varying designs.
How to Choose the Right Label Roller for Your Business
Selecting the right label roller involves several considerations that are essential to your packaging process:
- Production Volume: Assess how many products you need to label daily. For high-volume production, a fully automatic option may be the best choice.
- Label Size and Shape: Ensure that the label rollers you consider can accommodate the sizes and shapes of labels you use.
- Type of Product: Different products (such as cylindrical, flat, or irregular shapes) may require specialized roller types to ensure effective application.
- Budget: Balance the features of the label roller with your budget. Remember that while manual options are cheaper upfront, automation could save money in labor in the long run.
- Space Constraints: Ensure that you have adequate space for the machine and assess the workflow of your packaging operation to integrate it smoothly.
Integrating Label Rollers into Your Packaging Operations
Successfully integrating label rollers into your packaging operations requires a strategic approach:
- Training Staff: Proper operator training is essential to maximize the benefits of your new labeling system.
- Maintenance: Regular maintenance checks should be scheduled to ensure that the rollers remain in optimal condition, preventing costly downtime.
- Testing: Conduct tests to verify that the labels are applied correctly and meet quality standards before mass production.
- Feedback: Encourage feedback from your labeling team to identify any issues and optimize workflow.
Shineben: Your Trusted Partner in Packaging Equipment
At shineben.com, our commitment to providing high-quality packaging solutions is paramount. We understand the impact that efficient labeling has on your product presentation and brand perception. Our selection of label rollers encompasses various models tailored to meet your specific business needs.
With a focus on innovation, our label rollers are designed with the latest technology to ensure you stay ahead in the competitive market. Whether you need manual, semi-automatic, or fully automated solutions, we have the expertise and equipment to elevate your packaging process.
Conclusion: The Future of Packaging with Label Rollers
The adoption of advanced tools like label rollers is no longer optional; it’s a strategic necessity for businesses aiming to enhance their packaging efficiency and brand presentation. By understanding the benefits, types, and best practices associated with label rollers, companies can position themselves for unprecedented growth and success.
Investing in quality packaging equipment from shineben.com ensures you have the support you need in this competitive market. Embrace the future of packaging and unlock the potential of your business today.