The Impact of Injection Plastics on Metal Fabrication
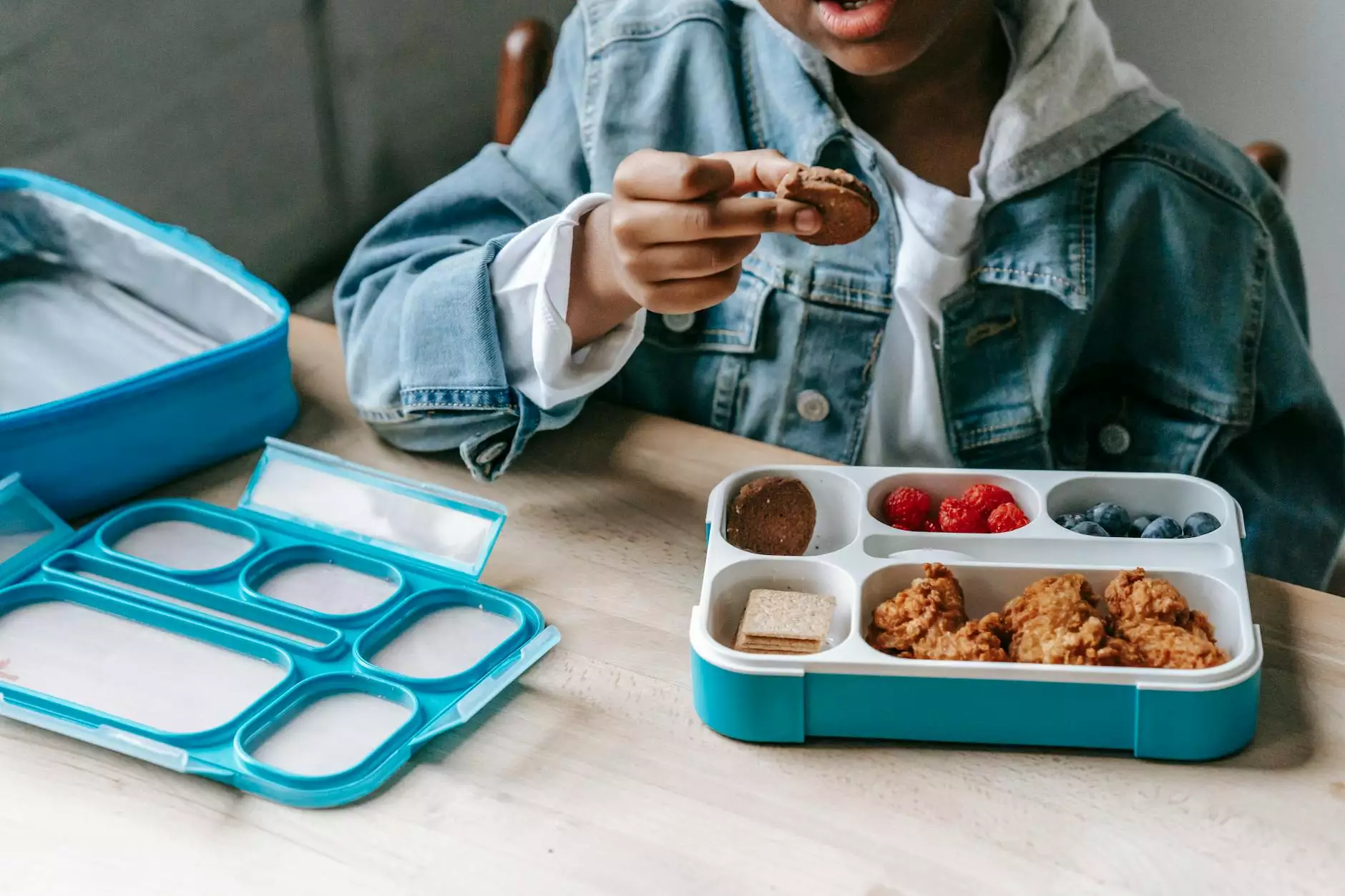
In the ever-evolving landscape of manufacturing, injection plastics have emerged as a game-changer, particularly in the realm of metal fabrication. This article delves deep into the intersection of these two processes, examining how the integration of injection molding technology with metal fabrication can lead to enhanced efficiencies, reduced costs, and improved product quality. As businesses like Deep Mould continue to innovate, understanding the synergy between these methods is crucial for companies looking to stay competitive.
Understanding Injection Plastics
Injection plastics involve a manufacturing process where molten plastic is injected into a mold to create precise shapes and components. This process is widely used due to its ability to produce complex designs with remarkable accuracy and repeatability. Some of its key benefits include:
- High Efficiency: Injection molding allows for rapid production cycles, significantly reducing lead times.
- Minimal Waste: The process is highly efficient, using only the necessary amount of material.
- Versatility: A wide range of plastics can be used, allowing for customization to meet various application needs.
- Cost-Effectiveness: High-volume production can lower per-unit costs dramatically.
Metal Fabricators: The Backbone of Modern Manufacturing
Metal fabricators are integral to various industries, providing essential components for both consumer and industrial products. Their expertise lies in transforming raw metal into finished products through processes such as cutting, bending, welding, and assembly. The challenges faced by metal fabricators include:
- Material Costs: Fluctuations in metal prices can greatly affect profitability.
- Labor Shortages: Finding skilled labor remains a significant challenge in the industry.
- Quality Control: Ensuring high-quality standards while maintaining production efficiency is crucial.
- Technological Advancements: Staying ahead of technology trends is essential to compete.
The Convergence of Injection Plastics and Metal Fabrication
The combination of injection plastics and metal fabrication has the potential to revolutionize product development. By integrating plastic components with metal structures, manufacturers can achieve lightweight designs without sacrificing strength. Here are some applications where this synergy is particularly effective:
- Hybrid Products: Many industries, including automotive and electronics, are increasingly using hybrid components made from both metal and plastic. This combination can reduce weight and improve fuel efficiency in vehicles while lowering costs in electronics.
- Enhanced Functionality: Incorporating plastic parts can provide additional functionality, such as insulation, vibration dampening, or improved aesthetics.
- Reduced Assembly Time: Utilizing injection-molded plastics can streamline the assembly process, allowing for fewer components to be put together.
Advantages of Using Injection Plastics in Metal Fabrication
Integrating injection plastics into metal fabrication processes offers numerous advantages for manufacturers, including:
1. Cost Reduction
Utilizing plastics can lead to significant cost savings in production, particularly when large volumes are produced. The lower costs of raw materials compared to metals further enhance profitability.
2. Improved Product Design
Injection molding techniques enable designers to create more complex shapes and features that may be difficult or expensive to achieve with metal alone. This flexibility fosters innovation and creativity.
3. Lightweight Solutions
In today's market, weight reduction is a critical factor, especially in industries like automotive and aerospace. Merging metals with plastics can produce lightweight yet durable products, directly impacting energy consumption and efficiency.
4. Enhanced Durability and Resistance
Combining metals and plastics can result in products that are resistant to corrosion and wear, prolonging their lifecycle and reducing maintenance costs. Advanced plastics can withstand extreme environments that metals may not endure as effectively.
Case Studies: Successful Integrations of Injection Plastics in Metal Fabrication
Real-world applications illustrate the successful integration of injection plastics in metal fabrication. Here are a few noteworthy examples:
Automotive Parts
In the automotive industry, manufacturers have begun to produce hybrid components utilizing both metal and plastic. For example, car manufacturers are adopting plastic bumpers and metal reinforcements to enhance safety and reduce weight.
Consumer Electronics
Electronics companies are utilizing injection molding to create casings that are both lightweight and appealing. The integration of plastic components can reduce assembly time and improve the overall customer experience through enhanced product features.
Medical Devices
The medical field has seen substantial benefits from combining injection plastics with metals. Devices requiring sterile conditions and ergonomic designs leverage this synergy to create innovative, safe, and effective products.
Challenges and Considerations
Despite the numerous benefits, there are challenges that businesses might face when integrating injection plastics with metal fabrication. Consider the following:
Material Compatibility
Understanding the compatibility of different materials is crucial. Some plastics may not adhere well to metals, requiring specific treatments or coatings to ensure a strong bond.
Technology Investment
To effectively implement this integration, companies may need to invest in new technology and training, which can be a barrier for some.
Regulatory Compliance
In industries such as medical and automotive, ensuring compliance with regulations on materials and design can complicate the integration process.
The Future of Injection Plastics and Metal Fabrication
As the demand for lighter, more efficient products continues to grow, the role of injection plastics in metal fabrication is poised to expand. Innovations in materials science, design software, and manufacturing processes will drive this growth. Key trends to watch include:
- 3D Printing: This technology can complement injection molding by allowing for rapid prototyping and custom parts that can be easily integrated.
- Sustainability: The push for eco-friendly materials and processes will lead to the development of biodegradable plastics and recyclable composite materials.
- Automation: Robotics and automation technologies will streamline production processes, enhancing efficiency and reducing labor costs.
Conclusion
The convergence of injection plastics and metal fabrication is not just an emerging trend; it is a compelling necessity for businesses looking to thrive in a competitive landscape. With its myriad of benefits ranging from cost savings to enhanced product design, this integration represents the future of manufacturing. As companies like Deep Mould lead the charge in this innovative space, it is crucial for others to understand and embrace these technologies to remain relevant and competitive.