Understanding High Vacuum Systems in Business Operations
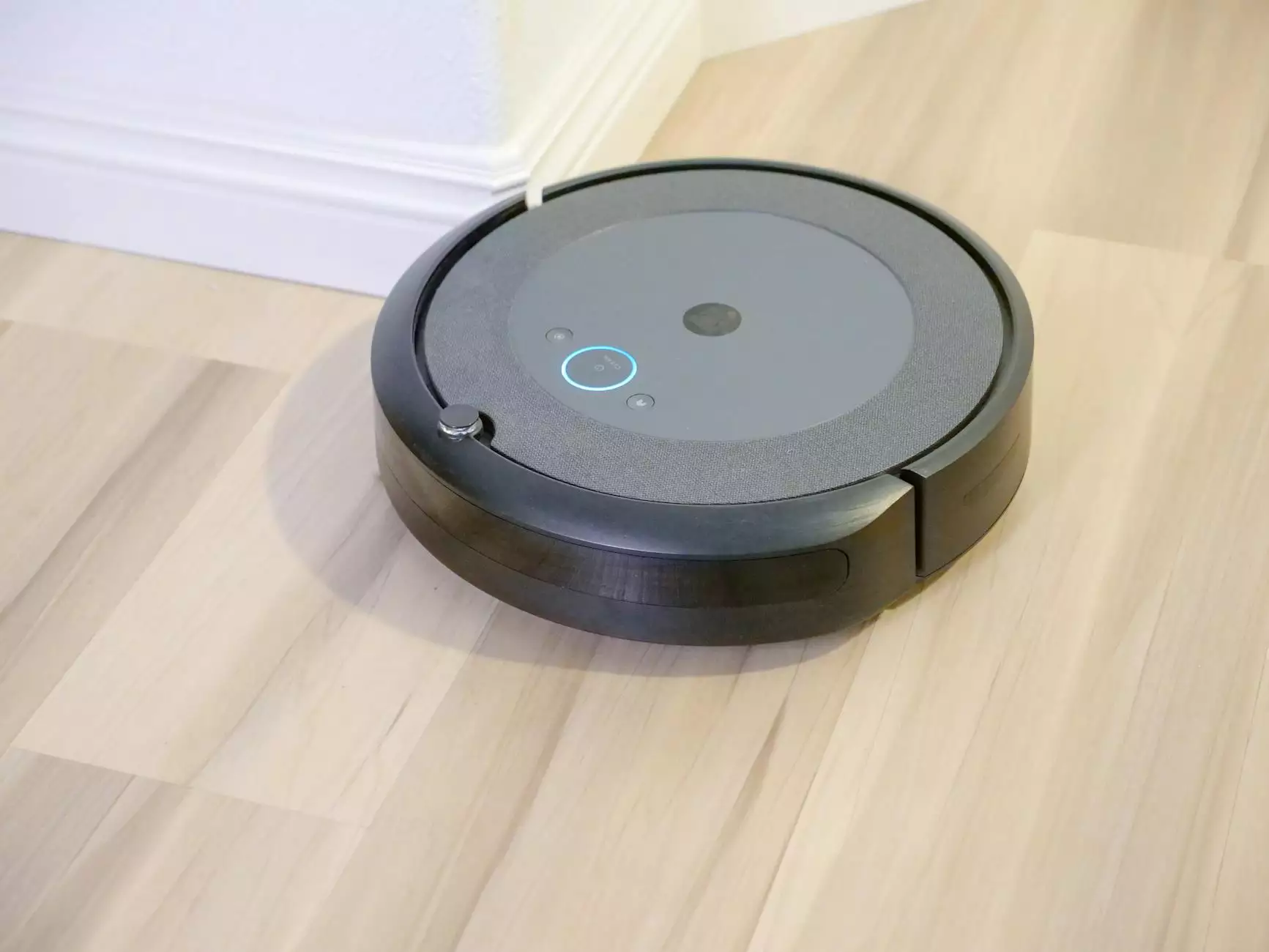
High vacuum systems play a crucial role in various industrial applications, where maintaining a controlled, low-pressure environment is essential. These systems are particularly significant in sectors such as electronics, pharmaceuticals, and extensive manufacturing operations. In this article, we will delve into the intricacies of high vacuum systems, their functionalities, importance, and application in enhancing business efficiency.
What is a High Vacuum System?
A high vacuum system is designed to create a vacuum in which the pressure is significantly lower than atmospheric pressure. This is typically defined as a pressure below 10^-3 Torr. The creation of such vacuums is crucial in processes that require the elimination of air and other gaseous contaminants that may interfere with production or experiments.
Components of High Vacuum Systems
High vacuum systems consist of various components, each playing a pivotal role in achieving and maintaining the desired vacuum level:
- Vacuum Pumps: These are essential for evacuating air from a chamber. There are various types of vacuum pumps, including rotary vane pumps, turbomolecular pumps, and diffusion pumps.
- Vacuum Chambers: These are sealed environments where the vacuum is created. They are designed to withstand external atmospheric pressure.
- Valves: These control the entry and exit of gases within the system and ensure that the vacuum is maintained effectively.
- Vacuum Gauges: Instruments that measure the quality and level of vacuum within the system.
Applications of High Vacuum Systems in Business
High vacuum systems are utilized across various industries due to their ability to improve process reliability and product quality. Here are some notable applications:
1. Semiconductor Manufacturing
In the semiconductor industry, precision and quality are paramount. High vacuum systems are integral to the fabrication of microchips, where they help create a contamination-free environment critical for photolithography and etching processes. By maintaining a high vacuum, manufacturers can ensure a cleaner substrate and enhance device performance.
2. Pharmaceutical Production
Pharmaceutical manufacturing often uses high vacuum systems for processes such as lyophilization (freeze-drying). This technique removes moisture from products without altering their chemical composition. The high vacuum conditions ensure that the product remains sterile and effective, which is essential in the production of vaccines and sensitive medications.
3. Vacuum Packaging
High vacuum systems are widely used in food processing to create vacuum-sealed packaging. This method prolongs shelf life by preventing oxidation and the growth of spoilage organisms, thereby providing quality assurance for consumers and reducing waste for businesses.
4. Research and Development
In research facilities, high vacuum systems are crucial for experiments in material science, physics, and chemistry. They allow scientists to study behaviors and reactions in a controlled environment, leading to innovations and advancements in technology.
Advantages of Implementing High Vacuum Systems
Understanding the advantages of high vacuum systems can help businesses realize their importance in enhancing operational efficiency:
- Improved Product Quality: The elimination of air and contaminants leads to higher-quality products with fewer defects.
- Enhanced Efficiency: Processes operating in high vacuum conditions often require less time, thereby increasing overall productivity.
- Cost Reduction: By minimizing material waste and energy consumption, businesses can significantly lower operational costs.
- Increased Safety: Maintained high vacuum environments reduce the risk of explosive reactions, making the process safer for employees.
Implementing a High Vacuum System
Implementing a high vacuum system into a business’s operations involves careful planning and consideration. Here are the steps to ensure a successful installation:
1. Assessing Business Needs
Before purchasing a high vacuum system, it's vital to assess your specific operational needs, including:
- The type of processes that will utilize the vacuum.
- The required vacuum level and performance specifications.
- Space and location for installation.
2. Selecting Appropriate Equipment
Choosing the right equipment is critical. Considerations include:
- Type of vacuum pump.
- Material of the vacuum chamber.
- Valves and gauges needed for your specific application.
3. Installation and Maintenance
Professional installation is recommended to ensure optimal functionality and safety. Following installation, regular maintenance is crucial to:
- Monitor system performance.
- Identify any wear and tear on components.
- Ensure seals and connections are intact to prevent vacuum loss.
Conclusion
High vacuum systems are indispensable for modern businesses that seek to enhance product quality, efficiency, and safety. As industries continue to evolve, the significance of these systems will undoubtedly grow. By integrating high vacuum technologies, businesses not only improve their production processes but also position themselves as leaders in innovation within their respective sectors.
Investing in high vacuum systems is not just about adhering to current industry standards, but about paving the way for future advancements. Whether it's through improving manufacturing processes or ensuring product integrity, businesses can reap significant benefits from these sophisticated vacuum technologies.
For more information about high vacuum systems and to explore the latest technology available, visit TMM.