Understanding the Role of a Diesel Engine Manufacturer
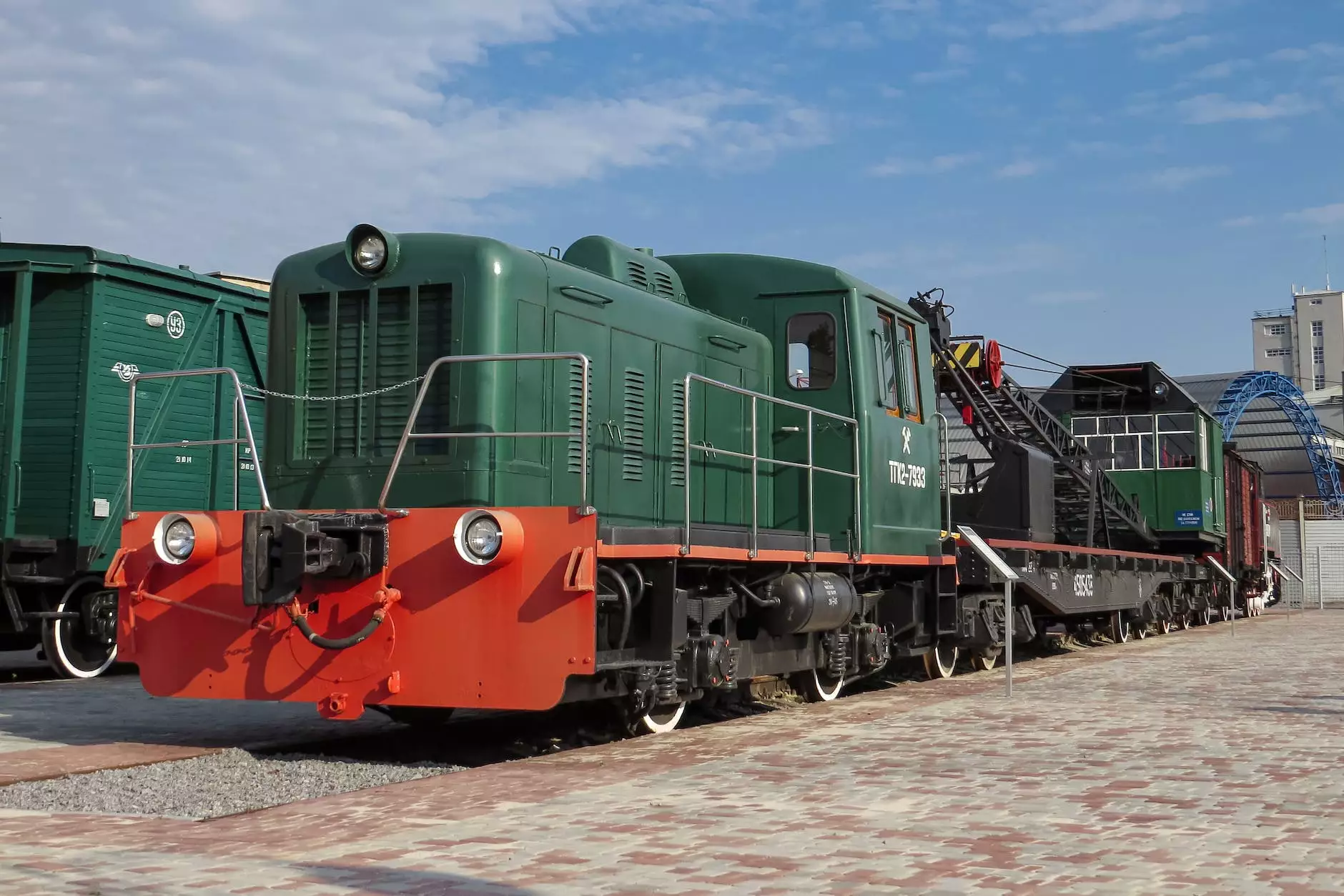
Diesel engines are indispensable in various sectors, including transportation, construction, and energy production. As a result, the role of a competent diesel engine manufacturer becomes paramount in ensuring that these engines meet the rigorous demands of their applications. In this comprehensive article, we explore the significance of diesel engines, the manufacturing process, and the key factors to consider when choosing a manufacturer.
Why Choose Diesel Engines?
Diesel engines are renowned for their efficiency, durability, and power. Here are several reasons why many industries prefer diesel engines:
- Fuel Efficiency: Diesel engines generally provide better fuel economy compared to gasoline engines, which translates to lower operational costs.
- Torque and Power: These engines deliver higher torque at lower RPMs, which is beneficial for heavy machinery and vehicles.
- Longevity: With proper maintenance, diesel engines can have substantially longer lifespans than their gasoline counterparts.
- Lower CO2 Emissions: While diesel engines emit other pollutants, they typically produce less carbon dioxide per unit of energy produced, contributing to a lesser greenhouse effect.
The Manufacturing Process of Diesel Engines
The manufacturing process of diesel engines is a sophisticated journey involving multiple stages. Understanding this process is vital for appreciating the quality and performance of the final product. Here are the key steps:
1. Design and Engineering
This initial phase involves comprehensive market research and the application of advanced engineering principles to create an efficient engine blueprint. Engineers utilize computer-aided design (CAD) software to ensure precision in every aspect of the engine's design.
2. Material Selection
Choosing the right materials is critical. Manufacturers typically use robust materials such as cast iron and aluminum alloys, which provide the necessary strength and heat resistance. This selection is crucial for the longevity and efficiency of the diesel engines.
3. Component Manufacturing
Once materials are selected, the manufacturing of individual components, such as the crankshaft, pistons, and cylinder heads, commences. Advanced techniques like machining, casting, and forging are employed to create these components with high accuracy.
4. Assembly
After components are manufactured, they are assembled in a controlled environment. Skilled technicians meticulously assemble the engine, ensuring that every part fits perfectly. Quality control takes center stage during this phase to avoid any defects.
5. Testing
The final engines undergo rigorous testing protocols to ensure functionality, reliability, and safety. Tests often include performance testing, emissions testing, and durability trials. Only engines that meet all specified criteria are approved for sale.
Key Considerations When Choosing a Diesel Engine Manufacturer
Selecting the right diesel engine manufacturer is critical for ensuring the success of your projects. Here are some important factors to consider:
1. Experience and Reputation
Look for manufacturers with extensive experience in the field. A reputable manufacturer will provide case studies or references from previous clients. Check reviews and industry ratings to gauge their standing.
2. Quality Certifications
Ensure that the manufacturer adheres to quality assurance standards such as ISO 9001 or equivalent. Certifications indicate a commitment to quality and consistency in their manufacturing process.
3. Research and Development
Choose a manufacturer that invests in research and development. This commitment leads to innovation and improvements in engine performance, efficiency, and sustainability.
4. After-Sales Support
Evaluate the after-sales services offered, including maintenance, warranties, and availability of spare parts. A reliable manufacturer should provide comprehensive support throughout the engine's operational life.
5. Customization Options
Not all applications require the same type of diesel engine. Look for manufacturers who offer customization options to tailor the product to your specific needs.
The Future of Diesel Engines
The future of diesel engines is bright, despite the technological and regulatory shifts towards more eco-friendly solutions. Many manufacturers are focusing on developing clean diesel technology, which aims to reduce emissions while improving performance. Technologies such as selective catalytic reduction (SCR) and diesel particulate filters (DPF) are already making waves in the industry, helping diesel engines to meet stringent emission regulations.
Innovation in Diesel Engine Design
Innovation plays a crucial role in the evolution of diesel engines. The integration of smart technologies and the Internet of Things (IoT) will continue to enhance engine performance. Manufacturers are exploring options like electric hybrid systems, where electric motors assist diesel engines, providing an eco-friendlier alternative.
Conclusion: The Value of a Reliable Diesel Engine Manufacturer
In summation, the choice of a diesel engine manufacturer can significantly impact operational efficiency, cost-effectiveness, and project success. Industry players must prioritize quality, innovation, and support when selecting a manufacturer to partner with. Investing in high-quality diesel engines manufactured by a reputable supplier such as Engine Family ensures that your machinery operates reliably, efficiently, and sustainably, setting your business up for long-term success.
Explore the offerings of top manufacturers, compare their specifications, and make an informed decision that aligns with your business needs and environmental goals.