The Comprehensive Guide to Plastic Injection Products
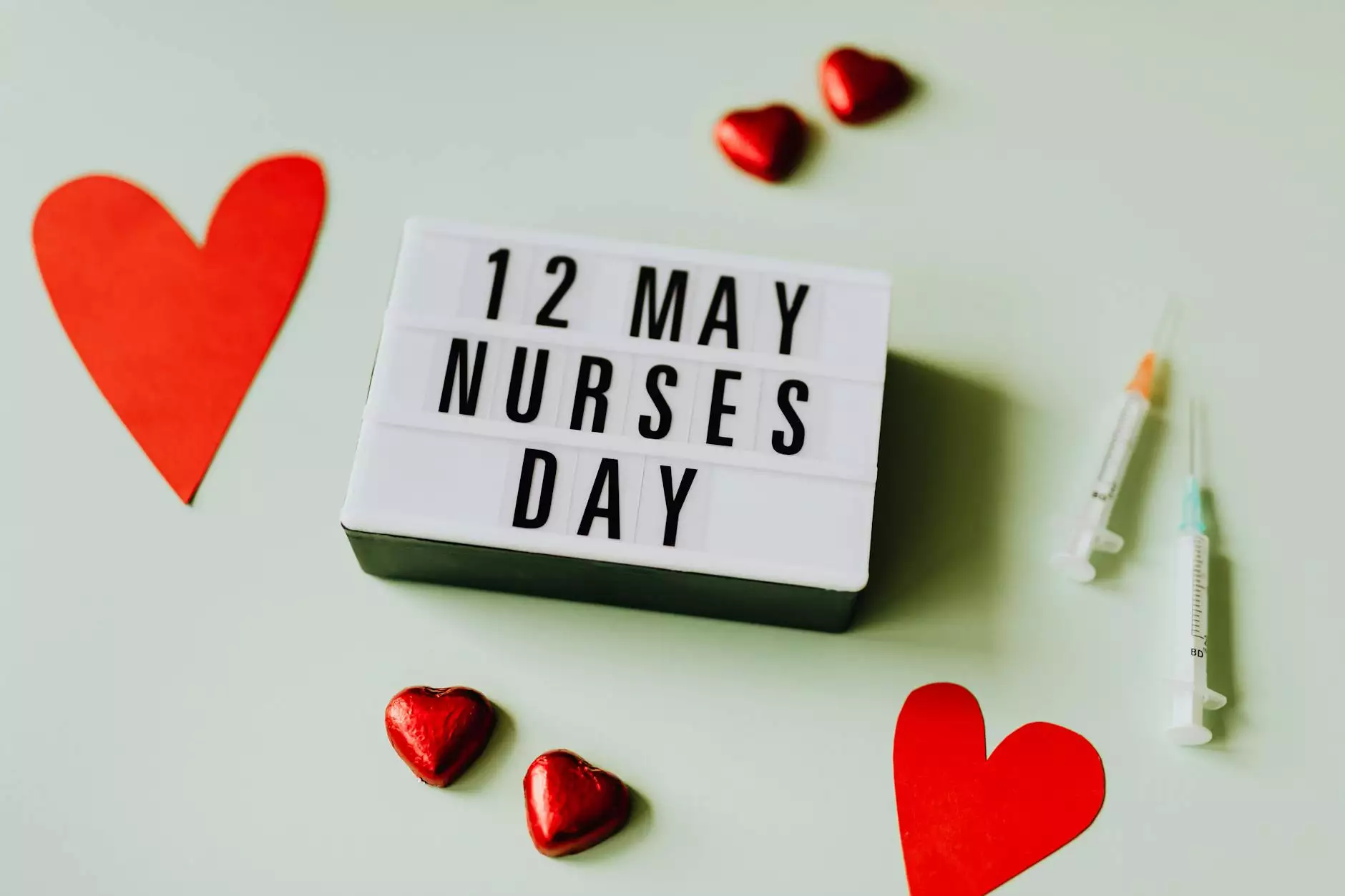
Understanding Plastic Injection Products
In today’s rapidly evolving industrial landscape, plastic injection products play a crucial role in manufacturing and design. This process allows for the creation of intricate parts and components, making it a preferred choice across multiple industries. From automotive to consumer electronics, the impact of plastic injection molding is profound and far-reaching.
What is Plastic Injection Molding?
Plastic injection molding is a process used to manufacture parts by injecting molten plastic into a mold. This technique enables the production of a wide variety of products, ranging from simple designs to complex components. The process is highly efficient and allows for the creation of high volumes of parts with remarkable precision.
The Process of Plastic Injection Molding
The plastic injection molding process can be broken down into several stages:
- Material Selection: Choosing the right type of plastic is essential for the desired product characteristics.
- Mold Design: Creating a mold that will ensure the final product meets specifications and quality standards.
- Melting the Plastic: The plastic pellets are heated until they reach a molten state.
- Injection: The molten plastic is injected into the mold cavity under high pressure.
- Cooling: The plastic cools and solidifies into the mold shape.
- Mold Removal: Once cooled, the mold is opened, and the finished part is ejected.
Benefits of Plastic Injection Products
Plastic injection products offer numerous advantages that make them ideal for various applications:
- High Efficiency: The process allows for rapid production rates, making it suitable for large volumes.
- Precision and Consistency: Injection molding provides a high level of detail and consistency across production runs.
- Material Versatility: A wide range of plastics can be used, each with unique properties suitable for diverse applications.
- Cost-Effective: While the initial investment in molds can be high, the per-unit cost decreases significantly with volume production.
- Reduced Waste: The injection molding process produces minimal waste when designed efficiently.
Applications of Plastic Injection Products
The versatility of plastic injection molding allows it to address needs across various sectors:
1. Automotive Industry
In the automotive sector, plastic injection products are used for dashboard components, exterior trim, and engine parts, significantly reducing weight and improving fuel efficiency.
2. Consumer Electronics
Everyday gadgets, from smartphones to TVs, utilize parts produced through injection molding, ensuring durability and aesthetic appeal.
3. Medical Devices
Injection molding creates components for medical devices, offering precision and compliance with strict safety standards.
4. Industrial Applications
Plastic injection products are essential in manufacturing tools, equipment housings, and various industrial components.
5. Household Goods
Many everyday items, including kitchen utensils and storage containers, are manufactured using plastic injection molding.
Quality Manufacturing Standards
To ensure the reliability and safety of plastic injection products, manufacturers must adhere to rigorous quality control standards:
ISO Certification
ISO (International Organization for Standardization) certification is critical for manufacturers striving to demonstrate their commitment to quality and continuous improvement.
Material Compliance
All materials used in production must comply with industry standards, ensuring safety, health, and environmental protection.
Regular Testing
Components are regularly tested for durability, strength, and compliance with design specifications to meet customer demands.
Challenges in Plastic Injection Molding
Despite its advantages, there are challenges associated with plastic injection molding that manufacturers must navigate:
1. Initial Costs
The upfront investment in molds and machinery can be substantial, making it necessary to evaluate long-term production needs.
2. Design Complexity
Creating molds for complex designs can be challenging and might require advanced engineering solutions.
3. Cycle Time Constraints
Minimizing cycle times while maintaining quality is a constant balancing act in production.
Choosing the Right Manufacturer for Plastic Injection Products
When selecting a company for plastic injection products, consider the following factors:
- Experience and Expertise: Look for a manufacturer with a proven track record in your industry.
- Advanced Technology: Ensure they utilize modern machinery and techniques for efficiency and quality.
- Customer Service: A responsive team that understands your needs can drive the success of your projects.
- Comprehensive Services: Select a manufacturer that offers end-to-end services, from design to delivery.
- Competitive Pricing: While cost is important, consider the total value of the services provided.
The Future of Plastic Injection Products
The future of plastic injection products is promising. With advancements in technology such as 3D printing integration, the potential for bioplastics, and improved recycling techniques, this industry is poised for innovation.
Moreover, as sustainability becomes increasingly important, manufacturers are adapting to reduce their environmental impact. Using recycled materials and developing eco-friendly plastics will be pivotal for future growth.
Conclusion
In conclusion, the importance of plastic injection products in manufacturing cannot be overstated. They offer unparalleled benefits and are integral to diverse industries. By choosing quality manufacturing partners and staying abreast of industry trends, businesses can succeed in leveraging plastic injection molding for their product needs. The horizon looks bright for this innovative technique, aiming to enhance efficiency, reduce costs, and meet the demands of a changing market.
If you are looking for reliable and high-quality plastic injection products, consider visiting Sumiparts.us to learn more about their comprehensive services and solutions.